New wood floors procedure
Samuel Go lightly
14 days ago
Related Stories
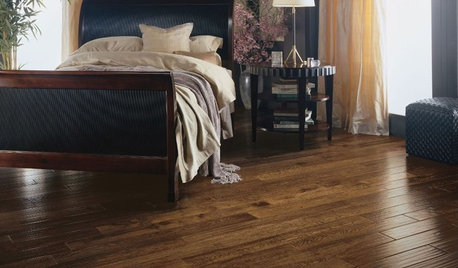
REMODELING GUIDESYour Floor: An Introduction to Solid-Plank Wood Floors
Get the Pros and Cons of Oak, Ash, Pine, Maple and Solid Bamboo
Full Story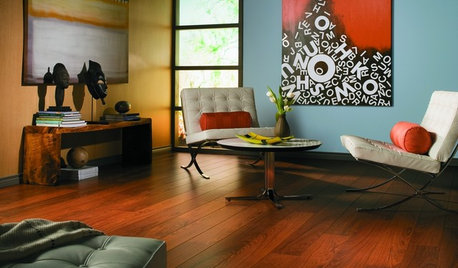
REMODELING GUIDESLaminate Floors: Get the Look of Wood (and More) for Less
See what goes into laminate flooring and why you just might want to choose it
Full Story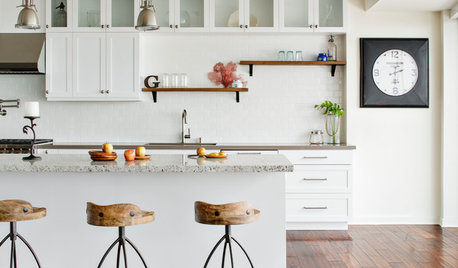
REMODELING GUIDESWhat to Know About Engineered Wood Floors
Engineered wood flooring offers classic looks and durability. It can work with a range of subfloors, including concrete
Full Story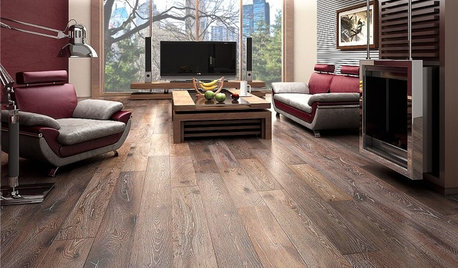
REMODELING GUIDESWhen to Use Engineered Wood Floors
See why an engineered wood floor could be your best choice (and no one will know but you)
Full Story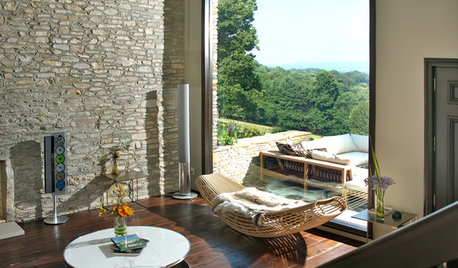
REMODELING GUIDESYour Floors: Zebra, Tiger, and Teak Wood, Oh, My!
Get the Pros and Cons of Exotic Woods: Hickory, Cherry, Rosewood and More
Full Story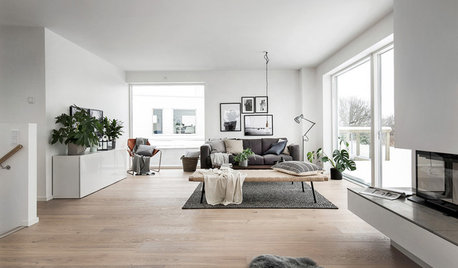
DECORATING GUIDESIsn’t It Good, Nordic Wood: The Appeal of Pale Floors
From silvery ash to honey blonde or chalk white, light-toned floors hold the key to the pared-back simplicity of Scandinavian style
Full Story
REMODELING GUIDESWood Floor Care: Polish Your Skills
Help your wood floors stay gorgeous by learning how to keep stains, dullness and warping at bay
Full Story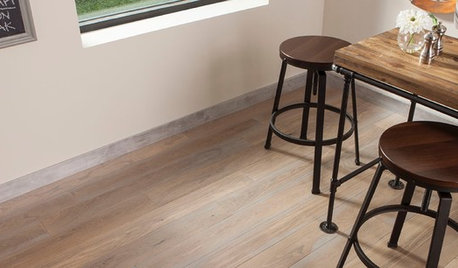
SHOP HOUZZTrade Pricing: Wood Flooring
Source real and engineered wood to lay a foundation that’s sturdy and stylish
Full Story0
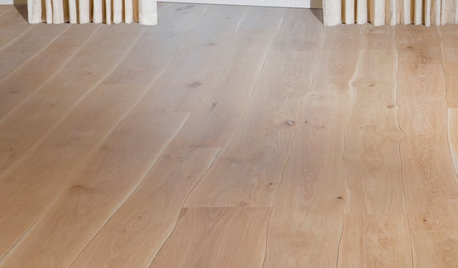
REMODELING GUIDES5 Innovative Wood Floors
Natural Forms? Wine Barrels? Peach Pits? Take a Look at Some New Ideas for a Warm Wood Floor
Full Story
HALLETT & Co.
Samuel Go lightlyOriginal Author
Related Professionals
Elmhurst Flooring Contractors · Green Bay Flooring Contractors · Miami Flooring Contractors · Oxford Flooring Contractors · Patterson Flooring Contractors · Redlands Flooring Contractors · Saint Paul Flooring Contractors · Severna Park Flooring Contractors · Waunakee Flooring Contractors · Pendleton Tile and Stone Contractors · Conway General Contractors · De Pere General Contractors · Marysville General Contractors · Panama City Beach General Contractors · Randolph General Contractorsmillworkman
G & S Floor Service
Samuel Go lightlyOriginal Author
G & S Floor Service
dan1888
Tish
Samuel Go lightlyOriginal Author
Minardi
dan1888
millworkman